1-W.O.G. (water, oil and gas) Oil Refineries, Natural Gas, Chemicals, Petrochemicals, Steam Pipes, Water Treatment, Chlorine, Paints, Food Industries and other related industries.
2- Wide range of operating temperatures from -50 Co up to 230 Co.
3- Above ground and under ground, also can be mounted horizontally or verticaly on the pipeline.
Options:
1- Operating:
In addition to standard handles MV is also available with:
– Vertical or horizontal Gear boxes.
– All Types of actuators.
– Special devices like “T” wrench.
2- Double Block & Bleed.
3- MV Valves are applicable above ground or under ground through some modifications
in the neck to avoid sand and soil particles penetration to the inside of the valve.
4- Pressure Releif System:
For evacuation of the ball cavity in case of volatile gases to releife excess pressure.
5- Locking Devices:
To avoid openeing or closing the valve by non-authorized persons.
6- Different End Types:
– Flanged.
– Threaded (inner or outer threaded).
– Welded (butt or socket weld).
7- qualival is capable of suppling special valves upon request (design and/or materials).
DESIGN FEATURES:
1-BALL (Solid ball) Fig 1
One of the most important components in any ball valve is the ball itself (the control element).
The sphericity and surface finish of the ball are directly related to the life time of the valve, its pressure-holding capability and the operating torque.
For these reasons balls are manufactured by a special process to give a final 3/5 RMS.
Surface finish and a sphericity of 0.0008″ The parallel bore off balls are manufactured in a standard, polished stainless steel 316.
Also availabale in carbon steel and stainless steel with ENP or nickel plated.
In case the valve is mounted to a chlorine service pipe-line the ball is manufactured with a pressure releife system to assure evacuation of the valve cavity.
MV flanged ball valves are manufactured with inserted seats in machined body recesses, to prevent seat movement and increaseseat life. MV flanged ball valves are manufactured with totally enclosedend/body seals (capsulated) to prevent cold flow, leakage and improve sealing.
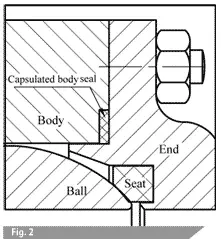
MV flanged ball valves feature:
(V) Style Stem packing multiple pressure energized (V) shaped ring, which creates multiple points of contact for maximum sealing effectiveness.
This style of stem packing provides positivepacking adjustment control to compansate the operational wear. In MV flanged ball valves, the stainless steel stem is assembled from insidethe body. The stem flange (an integral part of the stem) prevents the stem from blowing out upon increasing the pressure within the body cavity. (anti-blow out stem) valves are fire safe as it prevents leakage in case of fire (it is considered fire safe stem packing).
Also allows replacement of stem packing while the valve is under pressure. (See the 3D video below)
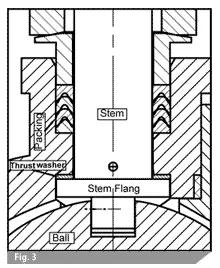
The stem assembly also provides full anti static capability for more safety. Stem design meets ANSI-B16.34 and BS 5351 (1986) (ISO 7121) specifications. (to discharge any static electricity to the pipe line earthing system.)
5-Gland, Stem Seal And Thrust Bearing (Fig.4).
MV flanged ball valves feature: a bolted gland of two-piece, self aligning type (seat ring and gland flange separate components). Bolted gland design meet BS 5351 specifications. Some MV ball valves incorporate a PTFE* (Pure teflon) thrust bearing seal to absorb any radial loading on the valve stem, to minimize gland to stem galling and assure smooth operation. This is a special important feature for actuated valves. RTFE**(Reinforced teflon) thrust bearing (washer) is also provided to reduce friction due to axial loading.
PTFE*: Poly tetra fluoroethylene.
RTFE**: Reinforced poly tetra fluoroethylene.
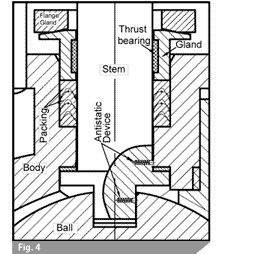
In addition to standerd adjustable stem valves qualival offers:
A – Standard product Provides predictable and constant packing by using cup springs which are tight permanently to store its spring force and restore it according to packing wear. (To compensate packing wear)
B-Optional with cover
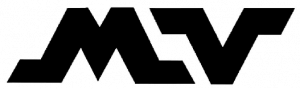
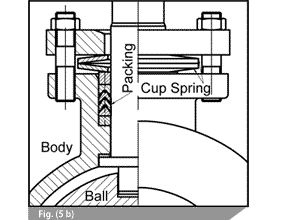
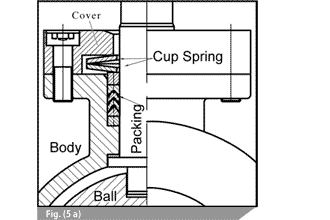
Integral mounting pad with drilled and tapped holes allows easy actuation in the factory or in the field to mount any type of oprating system: Gearbox, pneumatic actuator, electrical actuator etc. which are available uppon request.
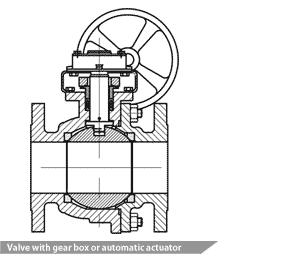
1- External leakage prevention:
a) Capsulated body seals: (Fig.2) As the body seal is located in a complete isolated cavity (capsulated), it is far away from the fire, i.e. it isn’t affected directly by the fire so it can keep its physical shape and hence its function for a considerable period Capsulated body.
b) Metal-to-metal sealing: Even if the body seal is destroyed by the fire, MV valve prevent external leakage. due to the wide metal-to-metal sealing surface between the body and the end as those contact surfaces are of a high surface finishing.
c) High quality assembly fasteners: The body is assembled to the end by studs according to: ASTM A 193 Gr. B7 (Gr. B8 for stainless steel valves).. And nuts according to ASTM A 194 Gr. 2H (Gr. 8 for stainless steel valves) This adds more rigidity.
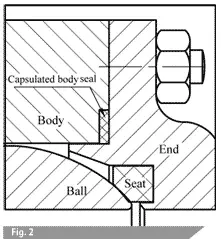
MV features no internal leakage at fire incident due to the presence of a second metallic seats (sharp edge) on which the ball sits after the damage of the Teflon seats, thus cuts the flow and prevent internal leakage.
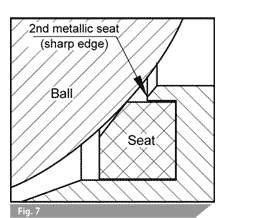
Hydrostatic shell test.
Hydrostatic seat test.
Low pressure gas seat test (leakage test).
10- Bore Design: Fig.8 (a & b)
According to the customers demand. The full bore or the reduced bore can be provided.
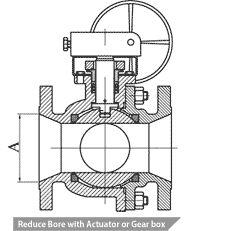
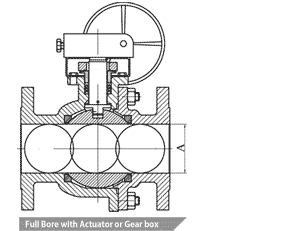
Emp-tying the valve by vent plug installed on the middle cavity to enable installing bleeding system and evacuate the valve allowing cleaning the pipe through bleeding the flow.
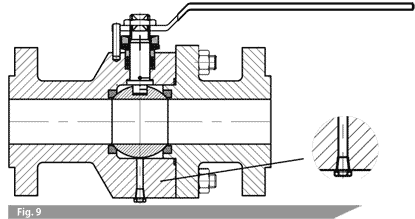
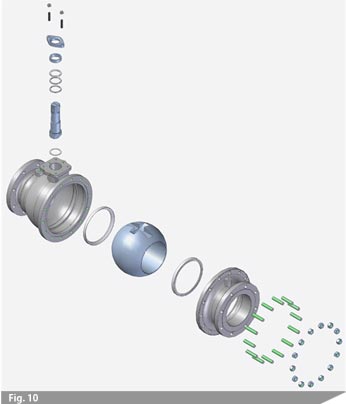
The ball is mounted by two supports:
The stem and trunnion mounted, so it can rotate freely.
The seat are floated with the action of set of springs located on insert ring so this action forces the seats to be in uniform contact with the ball surface
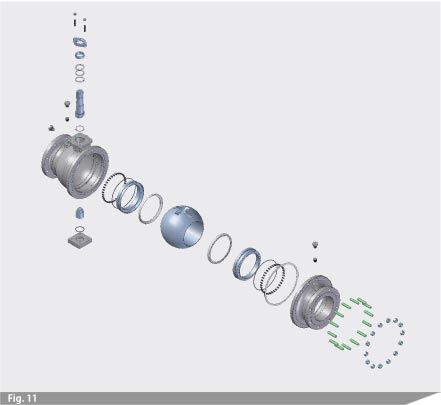
2- Trunnion support
3- Seat
4-Springs
5-Insert ring
6-Ball